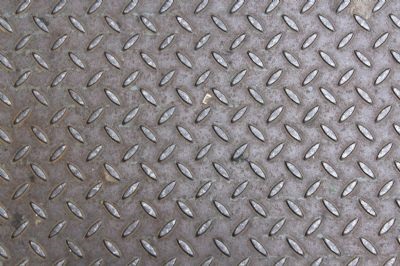
Whether it’s used to fabricate a small hand tool or a flatbed trailer, galvanized steel is the best defense against metal’s worst enemy: rust. “Galvanized” means the steel is metallurgically bonded with layers of zinc, a metal that is less likely to corrode. It can withstand atmospheric corrosion for many years with no maintenance, as zinc corrodes at a very slow rate. This makes it ideal for structures such as bridges, signs, water facilities and power plants.
Galvanization means longer life for the product, increasing the value of the steel. Even if it becomes scratched, the multiple layers of zinc will protect the area around the scratch for years to come.
Zinc is a naturally occurring metal, abundant in the Earth’s crust, and mined in several U.S. states as well as internationally. But the concept of using zinc to galvanize and strengthen other metals is not new. Galvanizing steel has been around for centuries — at least since the 1700s. The process is named after Italian physicist and physician Luigi Galvani, who conducted experiments using electricity and metals.
Although it costs more to purchase galvanized rather than “bare” steel, the economic benefits over the long term are clear, since it offers a lifetime of usage with minimal corrosion.
How is steel galvanized?
An object’s lifetime corrosion resistance depends greatly on how the zinc is applied. In short, the coating can be thick or thin.
Hot dip is the most effective method of galvanization — and it’s the one used for the trailers ALL purchased. During hot-dip galvanizing, steel or iron sheets are passed through a bath or vat of molten hot zinc, which bonds to the iron in the steel, forming a strong, protective barrier. The sheets can then be spun into different sizes without the zinc flaking off. How does ALL measure the value of choosing galvanized steel? The short answer: The value is measured in years.
Strong and reliable, galvanized steel is more expensive than regular steel, but these trailer decks will require less maintenance and be more resistant to chips, scratches, and wear, particularly corrosion caused by road salt and brine.
“We’ll see a great return on our investment in galvanized steel trailers,” said John Bacci, logistics director for the ALL Family of Companies. “Over the life of a trailer, we can do a lot in our shops to extend the life of our fleet — rebuild brakes, refurbish wood decks and electric lines, etc. But we won’t have to completely rebuild these new galvanized units because they are just that much more durable.”
The company estimates these trailers will remain a vital part of its fleet for three times longer than regular painted trailers.
“That’s a significant upgrade,” said Bacci. “This durability will not only make a positive impact for our northern branches that endure brutal winters, but also for branches in the Gulf region, where salty ocean air can really corrode metal.”
By investing in different types of steel trailers, ALL ensures the right equipment is available at each customer’s job site, for every variety of work and every geographic difference. This is what customers have come to expect from ALL — a commitment to ensuring the quality, longevity, and functionality of every piece of equipment they own.
Zinc is a naturally occurring metal, abundant in the Earth’s crust, and mined in several U.S. states as well as internationally. But the concept of using zinc to galvanize and strengthen other metals is not new. Galvanizing steel has been around for centuries — at least since the 1700s. The process is named after Italian physicist and physician Luigi Galvani, who conducted experiments using electricity and metals.
Although it costs more to purchase galvanized rather than “bare” steel, the economic benefits over the long term are clear, since it offers a lifetime of usage with minimal corrosion.
How is steel galvanized?
An object’s lifetime corrosion resistance depends greatly on how the zinc is applied. In short, the coating can be thick or thin.
Hot dip is the most effective method of galvanization — and it’s the one used for the trailers ALL purchased. During hot-dip galvanizing, steel or iron sheets are passed through a bath or vat of molten hot zinc, which bonds to the iron in the steel, forming a strong, protective barrier. The sheets can then be spun into different sizes without the zinc flaking off. How does ALL measure the value of choosing galvanized steel? The short answer: The value is measured in years.
Strong and reliable, galvanized steel is more expensive than regular steel, but these trailer decks will require less maintenance and be more resistant to chips, scratches, and wear, particularly corrosion caused by road salt and brine.
“We’ll see a great return on our investment in galvanized steel trailers,” said John Bacci, logistics director for the ALL Family of Companies. “Over the life of a trailer, we can do a lot in our shops to extend the life of our fleet — rebuild brakes, refurbish wood decks and electric lines, etc. But we won’t have to completely rebuild these new galvanized units because they are just that much more durable.”
The company estimates these trailers will remain a vital part of its fleet for three times longer than regular painted trailers.
“That’s a significant upgrade,” said Bacci. “This durability will not only make a positive impact for our northern branches that endure brutal winters, but also for branches in the Gulf region, where salty ocean air can really corrode metal.”
By investing in different types of steel trailers, ALL ensures the right equipment is available at each customer’s job site, for every variety of work and every geographic difference. This is what customers have come to expect from ALL — a commitment to ensuring the quality, longevity, and functionality of every piece of equipment they own.
# # #
Originally published as a sidebar: Spring 2015 Lift Line magazine